Navigation: | Home |
Building the Kimber Mill |
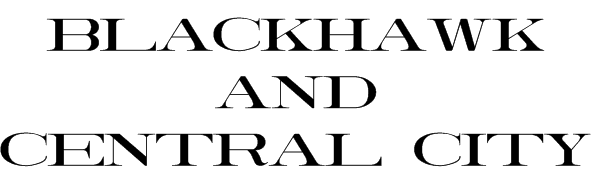 |
Building the Kimber Mill |
This page documents the Kimber Mill build - click on an image to see the full size
Background
This model was originally based on the description of the Kimber Mill provided on pp 101-102 of "The Gold Mines of Gilpin County, Colorado."
While there are no pictures of the mill available from the time period, the following points can be determined:
- The works were enclosed in a 95'x65' stone building.
- The mill had 32 stamps, eight Chilean Mills, and sixteen copper amalgamation tales.
- Power was provided by a 40 HP Woodury engine and a 23' diameter by 6' overshot water wheel.
From this description, my supposition is that the mill had four stamps per battery (rather than five as was used in later designs).
This can be confirmed by looking at this restored 19th century stamp mill.
In addition, that photo reveals the prototypical drop order was 2-1-3-4. So, the mill had eight batteries of stamps, each feeding
a copper table, which leads to a Chilean Mill and then to the second copper table.
But the story of the Kimber doesn't end there. One individual who read this description (and who has an interest in the history
of mining development) reached out to me privately and began researching this mill. His contention was that this was actually
the Polar Star Mill operating under a different name. Initially I disagreed, but as I uncovered more scraps of information,
I’m now in some agreement with him. Together, we’ve pieced together a history of the mill from 1868 up through the early 1900s.
One of the big challenges is that Job Kimber appears to have been a bit of a wheeler/dealer and had interests in many different
mills in the Colorado area. He was operating the one I’m looking to build in 1871 along with Garrott and Buffington. To further
confuse things, the mill appears to have first been constructed in 1867, an addition added in 1868, and then a further addition
added in 1870. So, it should end up being in three pieces, rather than a block structure (as I was previously designing).
On top of this, we uncovered that the stone building was erected in 1875 “over the old frame which was removed“, which indicated
that the outer building should be wood construction rather than stone.
At this point, more digging in the DPL turned up the following two photographs:
- From 1899. The important
part of the photograph for my purposes is the center right (showing the stone Kimber/Polar Star behind the square chimney:

- From 1870. Looking at
the center right, we find:

Most definitively a wooden frame, likely with a shingle roof, and certainly looking like a structure that had been built in
three pieces. So, I’ve pretty much torn up the old design and started on a new one, using Sketchup to help me visualize how
the floor plan and perspectives would look in three dimensions. The result is the following 3D perspective:
and a new set of (still incomplete) plans.
Could I Use A Commercial Model?
Having picked up a Durango Press DP-35 Gravity Stamp Mill kit, I did some research into some of the operational considerations
of a stamp mill, like the number of drops per minute, drop depth, drop height, depth of discharge in the mortar box (this is the
distance from the bottom of the mortar box to the bottom of the screen). For this, my source was "The Stamp Milling of Gold Ores."
In it, one finds that the DP-35 is a California style stamp mill, featuring a high-speed, short distance drop rate and a
shallow mortar box. On the other hand, Gilpin County mills featured a slower speed (30 drops per minute) longer distance drop
(typically 18") and a deeper mortar box (typically 14"). The reason for this is the higher percentage of pyrites in Gilpin County
rock. To separate the more tightly bound gold required the slurry to remain in the mortar box for a longer time (hence the
increased discharge depth) and be pulverized with a slower, longer stamp stroke. The bottom line of this is that the cams or
mortar box parts from the DP-35 won't work as masters, this build would require custom parts.
Water Wheel
The first subassembly to be built is the 23' x 6' overshot water wheel. These pictures detail the assembly process.
Sides are made from 1/32" aircraft plywood with an outer diameter of 23' (80.5 mm) and inner diameter of
21' (73.5mm). The wheel "bottom" is made from scribe sheathing cut to 23 mm in width and scribes turned in
to help the curvature |
 |
Add twelve 11' long (38.5 mm) 2"x6" spokes to each side. Rasp out a pocket on the wheel bottom to
receive each stake. In addition rasp out the inside edges of the spokes to edge glue them together.
Paddles start out as .012"x1/4" strip wood, cut to 6' length (21 mm long) and trim the width down from 1/4" to 5mm.
Incline the paddles by 5 degrees to the wheel and space a paddle every 10 degrees around the wheel. |
 |
Center drill a 3/32" hole in 1/4" brass rod and cut four hubs each .3 mm thick from stock and then mount
the hubs to the spokes using a 3/32" brass rod for alignment |
 |
Use two india ink/alcohol washes to stain the wood to model the water weathering. |
 |
Oops, after running through the operational considerations, I found
that I really should have paddles every 5 degrees around the wheel, so cut an additional 36, stain and insert into
the wheel. In addition, add a 3/32" shaft as an axle and weather metal parts with primer and grimy black |
 |
Add Grandt line NBWs where the spokes meet the outside of the wheel |
 |
The axle pillow blocks are from Crow River Products, and they fit the 1/16" brass axle. The pillow blocks
are mounted on custom 3-D printed sandstone pillars from Shapeways. |
 |
Flumes
The Mill has three flumes: one for delivering water to the wheel, one for carrying water from the wheel to the
mills, and one for carrying runoff.
Water Wheel Flume
The flume that delivers water to the wheel is made from 2"x6" planks with 6"x6" for bracing. It is also weathered with an India ink/alcohol wash. |
 |
The bent to support the flume is built from two 1/8" dowels and 2"x6" planks, with NBWs and the same India
ink/alcohol wash for weathering. |
 |
Run two 8"x10" stringers under the flume, weather them, and then attach the bent to the outside edge of the flume. |
 |
Flume from Wheel to Mills
The flume running from the wheel to the mills is constructed in three parts. The first part
consists of 2"x12" members forming a 30' base and edged with 3"x12". The two gaps are left to allow the
other parts to interlock. |  |
Three bents are needed to support the flume over the different floor heights. These are made from
square 8"x8", 10"x12" and 2"x6" for bracing and attached to 6"x6" strings on the underside of the flume. |
 |
Weather with more India ink/Alcohol |  |
The distribution channels are built from 3"x12" and notched to allow each flume to receive water. |
 |
The exit flumes are build from 2"x6" and 3"x6" in 8' sections. Weathering, once again is via an India ink wash. |
 |
Amalgamating Tables
The amalgamating tables have a slope of 2 1/8 inches per foot (or 10 degrees), a length of 12 feet and a breadth of 4 feet
(numbers taken from "The Stamp Milling of Gold Ores"). This section details how to build these tables.
Cut the 4.5' by 12.25' base from 1/32" plywood. Edge sides and bottom with 3"x3", leaving
a 1' space in the center of the bottom. Cut a 4'x12' piece of copper from 5 mil foil and mount to the base. |
 |
For the 10° incline, cut 3 pieces of 10"x12" to match the width of the table. Gang two of these
together to form a 10"x24". Then bevel the top edges and mount to the underside of the table. |
 |
Use two India Ink/Alcohol washes (one yellow and one black) to stain the basswood to look more
like weathered pine species found in the Gilpin County area and dress the copper table with Model Master Silver
to model the mercury dressing. |
 |
The last piece needed as a "fan out" from the Chilean mill to the lower table. This is made using 12"x12" and
6"x6" for the supports, 1/32" plywood for the base and 3"x3" for the edging |
 |
Batteries
Dimensions for the stamp mill batteries are based on those
specified in "The Stamp Milling of Gold Ores" coupled with those used in the DP-35 kit, with some license taken to
support construction.
For the batteries of stamp mills, dimensions chosen are based on those
Stamps are .022" brass wire cut 12' in length. The 8" d x 6" shoes are fabricated from 3/32" brass rod
with a center drill, cut to length and mounted to the end of the wire. Cam followers will be added later. |
 |
The vertical members of the T-braces are two pieces of 10"x12" cut to 16' in length and ganged together into a
10"x24" blank. The eight outside T-braces have a 14' base of 12"x12" material while the 4 inside T-braces use the same
length of 10"x12" for their base. |
 |
The Mortar Box Foundation consists of pieces of 2' long 12"x12" ganged together to match the width of the copper table.
These are stood on end and attached to a copper table. |
 |
Cut two pieces of 12"x12" 14' in length and use as footers under T frames to form batteries (each battery uses two outside and one
inside T brace). Space around the copper tables. |
 |
The Mortar Box bracing is a 12' piece of 10"x12" attached to the opposite side of the battery as the table 10" side down. |
 |
The Mortar Box is designed to be 18” deep, with a depth from the bottom of the box to the screen ledge of 14". Lastly, the
back of the box has an extension at 40 degrees to the vertical to model the copper plate used as part of the ore recovery system
(from "The Stamp Milling of Gold Ores"). The parts were fabricated at Shapeways.
|  |
500 Wire Mesh is used to model the discharge screen. |
 |
The wire mesh is cut to fit onto the screen ledge of each Mortar Box. |
 |
Adding the mortar boxes to the batteries, centering them with respect to the copper tables. |
 |
Cut two more pieces of 12"x12" 14' in length and inset 12" from the ends of the T-braces as the outside footers. |
 |
Stamp braces are made from three pieces of 10"x12": the first is notched to fit around the T braces and
the other two are cut to fit between the T braces and are mounted to the first piece. Drill out equally spaced
#65 holes for the stamps (the photograph shows a dry fit)
|
 |
Drill #75 holes for mounting NBWs where the T braces cross the footers and for the vertical support.
I use Grandt Line 2 1/4" nuts + 4 1/2" washers (catalog #5098)
|
 |
Cut three pieces of 10"x12" 5.75' in length. Miter the ends to 45 degrees and remiter the top to form
a support shelf for the lower stamp brace. Then mount to the T braces.
|
 |
Drill out 5/64" holes 4' up from the top of the short diagonal brace and cut 1/16" brass rod to fit
for the camshafts |
 |
18 inch drop cam from Shapeways |
 |
Fit the cams on to the camshafts |
 |
At this point, I realized that the mortar box was too low and the spacing between stamp shafts wouldn't work,
so I rebuilt the shaft braces using 3 mm spacing between shaft holes and raised up the mortar box/foundation and table
subassembly another scale foot and things look much better.
|
 |
The next step is to cut 6" scale cam followers from 18g hypodermic needle, insert them onto the stamp shafts,
position them against the cams and glue in place. |
 |
With the cam followers in place, the cams can now be set to the proper drop order (counting from the left 2-1-3-4)
and the top and bottom braces glued into place |
 |
Camshaft wheel
The camshaft wheel is its own small subproject:
Build a blank by edge gluing ten 7' long 8"x8" pieces together. Cut the wheel shape and drill out the center to 1/16". |
 |
Next, cut out two 28mm square blanks of .016" brass and cut out the hubs and rims from them. Drill out #75 holes in
the hubs every 45 degrees. |
 |
Attach the hubs and rims to the wooden center. Mark hole locations in the rim for the center of each board and drill out #75
holes. |
 |
Add 1 1/2" Grandt line NBWs (Catalog #5100) in each hole. |
 |
Mount the camshaft wheel on the camshaft. |
 |
Counter wheel
The counter wheel is also its own small build:
Begin with spare centers from 33" NWSL wheels (these were removed when making the 33" drivers for the engines).
Mount on 3/32" brass tubing, and machine the outside edge to uniform smoothness. Cut the brass tubing to length and then mount
on 1/16" brass tubing. Again cut to length and use 0.005" brass strips for the outside rim. Each battery gets its own
counterwheel.
|
|
Drill 1/32" holes in pillow blocks (I used ones from Scale Structures, catalog #2183), mount the counterwheel on 1/32" brass wire and thread
through the pillow blocks. Mount the pillow blocks to the bottom of each battery. |
|
Finishing up
With the cam wheels and counterwheels in place, all that remains is to add the long diagonal brace and finish up the NBWs.
Each battery gets three long diagonal braces. Cut a piece of 10"x12" 40 mm in length and bevel the two ends
at 30 and 60 degrees, keeping the long edge 40mm. Then mount on the back of the battery between the T and the base.
|
|
The next to last step is to add the rest of the NBWs according to the plans. |
|
The last step is to use two India ink/Alcohol washes (one yellow, one black) to stain the basswood to look like weathered pine and to paint the copper tables and the
back of the mortar box with Model Master Silver to model the mercury dressing |
 |
Chilean Mills
The Chilean Mills are made up from the following parts:
- Two 4' diameter by 10" sandstone rollers (beveled on the outside edge) built with 3D printing
- A 4' diameter sandstone platform built with 3D printing
- Two spindles that have a 21" by 4" diameter shaft with a 7" by 8" diameter head (3D printed too)
- A 10' long 1/16" brass tube for the central shaft
- A 17" long 3/32" brass tube sleeve, transverse drilled with #53 bit to mount the spindles
|
 |
Drill out the platform so that the central shaft fits and drill out the rollers so that the spindle fits.
Slide a sleeve over a central shaft, insert a spindle into a roller and use canopy glue to attach the spindle
end to the sleeve. Then repeat with a second spindle/roller on the other side of the sleeve. After the glue dries,
insert into the platform and test that the assembly rotates freely. |
 |
Carefully use primer and grimy black to paint the vertical shaft, sleeve and outside spindle hub |
 |
During operation, the rollers and pan of the Chilean mill are covered in mud, so the body gets dyed with
brown India Ink |  |
Supports for the vertical shafts are built from 12"x12" and 6"x6" bracing and weathered |
 |
To drive the mills, a pair of 4.5mm miter gears from gizmoszone.com are reamed out to 1/16" inch and
one is mounted on the vertical shaft. The other is mounted on a 1/16" rod along with a small pulley from
Crow River products that has also bean reamed out to 1/16" inch. Three pieces of weathered 12"x12" are used
as braces for the 1/16" rod and a large pulley cut from a 5/8" dowel and center drilled to
1/16" is mounted. The whole assembly is painted with Grimy Black. |
 |
Steam Power
A Crow River kit is used for the interior steam engine and assembled according to the instructions. |
 |
The steam boiler is a modified Horizontal Portable Boiler kit from Keystone Locomotive Works. From this kit,
the boiler, two end doors and stack are used. Glue doors to the ends of the boiler and use two pieces of 12"x12".
The stack is extended with a piece of 5/32" brass tube and the kit stack is carefully filed to fit into the end of
the tube. The whole assembly is painted grimy black. |
 |
The Mill Itself
For internal timbering, "Carpentry made easy" - 1868 indicates the following sizes were typical:
Main Timbers | 12 inches square |
Door Posts | 10 by 12 |
Purlin Posts | 8 by 10 |
Plates and purlin plates | 8 by 8 |
Braces | 4 by 6 |
Lower Joists | 3 by 12 |
Upper Joists | 3 by 10 |
Studding | 2 by 8 |
Rafters | 2 by 6 |
The 12"x12" main timbers are joined via lapped joints. The 12"x12" posts use .018" piano wire as a peg to keep
them square and aligned, and braces are 4"x6", beveled at 45 degrees and measuring 3 ft long point to long point |
 |
The floor of the mill is at two levels. The upper level measures 29'x90' and 1"x4" is used as planking.
An 18 gauge hypodermic is dipped in india ink/alcohol wash and used to mark nail holes on 24" centers. Extra
stain is acceptable for representing water staining.
|
 |
Mark the location of where the main timbers will pass through the floor and then drill and file these out.
After a test fit, mount the upper floor on 12"x12" and 8"x12" pieces stacked to provide 32" of height. This
provides the proper slope for the mill works. |
 |
Four sets of stairs provide links between the two floor levels. These use 1/32" plywood for support, 1"x12" for treads,
and 1"x6" for risers |
|
For the lower level of the floor, repeat the process used on the upper level of the floor and then attach
the stairs in place according to the building plans |
 |
The Roof Rafters
Roof rafters are 2"x6" spaced every 18". Use the rafter jig to shape the rafters from 30' pieces. |
 |
Use the jig to mark where the 8"x8" purlin is attached and use an 18" spacing jig to glue the purlin and ridge board in
place for one side of the roof section. |
 |
With enough rafters in place, cut the 8"x8" purlin post and 4"x6" brace and use the jig to fit together.
These are attached to the purlin where they will be brace against the main timbers. |
 |
Repeat with the other side rafters and then use the main timbers as guides to attach the two pieces. |
 |
The "original" roof and first addition rafters are turned 90 degrees to the section already constructed.
Use the second rafter jig to shape rafters from 22' and 16' pieces, attach these to 8"x8" purlins and
glue the two ridge boards together. Shape valler rafters for the place where the two roof sections join and attach
one end to where the ridge boards meet. |
 |
Finish out the rafters by using the jigs to shape jack rafters for the valleys |
 |
For the flume, cut open the roof rafters and add heads to both ends to create an opening for the flume. |
 |
Windows and Doors
Some more research on window pane size turns up "The Emigrant's Guide to the Western States of America" (1852) as a source, which
reports that a typical pane size was 10" x 13". Combining this size with the photo cited above turns up what appears to be
two windows in the original structure, each of 5x5 panels in size. The door openings in the photograph appear to be
consistent with a 3'x7' door, so we'll model that.
Start with the windowing jig |
 |
Fill in with 2"x2" (following rail/style practice). When glue sets up, remove and surround with
3"x8" to form the casing. |
 |
For the doors, cut two scale 3'x7' pieces from 1/64" plywood and surround with more 3"x8" to form the
casing. |
 |
Interior Walls
To keep water from the wheel splashing over operations, two interior walls are needed:
First, build and install stud supports - these are 2"x8" over a 2"x12" footer located on 18" centers |
 |
Repeat for the roof sections |
 |
The interior walls are cut from 1/64" plywood and shaped to fit. Cut openings for the doors, channels
and wheel axle |
 |
Add interior walls to the roof as well |
 |
More Assembly
Glue the lower flume, channels, and mills in place. |
 |
Glue the Chilean Mill assemblies into place |
 |
At this point, the Waterwheel and its supports can be installed, along with the main drive axle (1/16" brass)
and drive pulley. The axle, pillow blocks, and pulley are all painted grimy black. The prototypical speed of the waterwheel
would be 4 revolutions per minute, and 6 rpm for the Chilean mills, so the pulley diameters between the transfer
axle and the Chilean mils are in a 3:2 ratio. |
 |
The main transfer axle is build from two pieces of 1/16" brass, joined with a piece of 3/32" brass tube.
Pulleys and axle hangers are from Crow River Products and mounted on overhead beams. Everything is painted grimy black.
|
 |
Now install the lower tables and fans |
 |
Install the steam engine and use 20lb paper painted with Model Master's Leather paint and cut into 1/16"
strips for the leather belts - the twist ensures that the belt wears evenly. |
 |
The prototypical speed of the stamp mills would be 30 drops per minute - with two drops per revolution,
the camwheel rotates at 15 rpm. With the camwheel being the size that it is, I decided to use an auxiliary transfer axle
that would rotate at 30 rpm (the pulley ratio from the Chilean Mill to the auxiliary axle is 5:1 and the pulley
ratio from the auxiliary axle to the camwheel being 1:2). In addition, the belt between the Chilean mill and the
transfer axle is strung in a figure eight to reverse the rotation from clockwise (the direction the water wheel,
main transfer axle and Chilean mills all use) to count-clockwise (the direction needed for the camwheels). |
 |
Install the stationary boiler. Then bend two pieces of brass wire (0.052" and 0.040") to form the pipes between
the boiler and the engine, paint grimy black and install. |
 |
The 2"x8" studs are installed on 18" centers and sit on 2"x12" footers. |
 |
Gable studs are also 2"x8" and are installed on 2"x12" footers to provide support when the roof is removed. |
 |
Sheathing
1"x12" lap siding is applied to the sides of the mill using a 10" reveal and 2"x6" and 3"x3" pieces for trim boards. |
 |
The lap siding is continued up along the gable ends, while 1"x8" is used for roof decking to support the metal roof |
 |
Two washes of Alcohol and India Ink are used for the first part of weathering siding (gables not shown) |
 |
The metal roof pieces were made from 10' long pieces of corrugated roofing from Campbell Scale Models cut to 3' width.
They are overlapped two corrugations and flashing and caps made from aluminum foil. |
 |
As metal roofs in this period were painted with linseed oil mixed with red oxide (the same formula as freight car paint),
the roof is weathered with freight box car red paint, thinned 5 to 1 with water |
 |
Lastly, the fieldstone foundation is plastic pattern sheet from JTT cut to size. Weathering consists of
painting (in order) with flat white and fresh gravel grey acrylics. Individual stones are tinted with combinations
of those two colors and raw sienna, burnt sienna, and payne's grey acrylics. Final weathering for the foundation
consists of a wash of brown india ink and alcohol (dirt from rain spatter) and black india ink and alcohol (mildew).
At the same time, the bottom three tiers of the siding is also given a wash of brown india ink and alcohol to model
rain spatter |
 |